Bei Fraunhofer in Stade: Dr. Dirk Niermann entwickelt Roboter für die Montage von CFK-Bauteilen
Von Wolfgang Becker
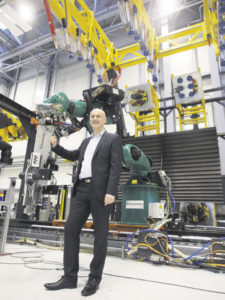
Dr. Dirk
Niermann steht
in der Versuchsanlage,
die im
Maßstab 1:1
Viertelschalen
von CFK-Rümpfen
zusammenfügen
kann. Die
Schalen werden
von Vakuumsaugnäpfen
gehalten,
die wiederum
auf Hexapoden
(sechsbeinigen
Robotern)sitzen.
Die größte Herausforderung
besteht
im Datenmanagement,
denn
der Prozess des
Zusammenfügens
wird über unzählige
Messdaten
gesteuert.
Foto: Wolfgang Becker
Der Name ist Programm: Fraunhofer-Institut für Fertigungstechnik und Angewandte Materialforschung IFAM – Klebtechnik und Oberflächen. Klingt so, als sei das jetzt ein Thema für Spezialisten, aber was da so sperrig daherkommt, ist in Wahrheit ein hochspannender Forschungsbereich, in dem Experten wie Dr. Dirk Niermann daran arbeiten, große Airbus-Bauteile aus CFK automatisch zusammenzufügen. Das Problem: Die geviertelte Rumpfschale für einen Airbus A350 wurde zwar in einem sehr präzisen Formwerkzeug gefertigt, aber die Aushärtung bei hohen Temperaturen bewirkt einen Verzug, der bei jedem Bauteil etwas anders ausfällt. Und: Wenn aus vier Vierteln eine Röhre werden soll, dann sind im Flugzeugbau Toleranzen von plus-minus 0,5 Millimeter akzeptabel – mehr nicht. Der Leiter des Bereichs Automatisierung und Produktionstechnik des in Bremen und Stade ansässigen Fraunhofer-Instituts entwickelt mit seinem Team im Forschungszentrum CFK die Produktionstechnologie von morgen. „Die großen CFK-Bauteile passen nicht ad hoc zusammen. Wir müssen sie aufspannen, nachbearbeiten und justieren. Das sind sehr zeitaufwendige Prozesse. Unser Ziel ist es, Roboter dazu zu bringen, dass sie die verschiedenen Bauteile beispielsweise einer Rumpfschale für den Airbus so zusammenfügen, dass sie exakt passen“, bringt er die Herausforderung auf den Punkt.
Wo muss ich messen?
Was einfach klingt, ist in der Umsetzung ein komplexes Forschungs- und Konstruktionsvorhaben. In der Halle des Forschungszentrums steht unter anderem eine große Versuchsanlage für die automatisierte Rumpfmontage. Das Projekt hat von der ersten Idee bis zum Aufbau des Prototyps bereits über eine Million Euro gekostet. Die Anlage befindet sich auf einer Skala von eins bis neun bereits im Reifegrad 6. Niermann: „Hier beantworten wir Fragen wie: Wo muss ich messen? Wie lassen sich Roboter mit Messwerten so steuern, dass die Rumpfbauteile präzise zusammengefügt werden? Wo setze ich die Sensoren an? Wir wollen mit Originalbauteilen zeigen, dass die Montage funktioniert.“
Wohlgemerkt: Hier wird handfeste Anwendungsforschung betrieben. Die Anlage ist für den CFK-Rumpf der A350 von Airbus ausgelegt, ließe sich aber genauso auch für die A320-Serie umrüsten – um die entwickelten Technologien auf weitere Anwendungsfelder zu übertragen. Die Fraunhofer-Forscher haben dazu einen modularen Aufbau gewählt, sodass beispielsweise auch die Bauteile von Seitenleitwerken zusammengefügt werden können. Ziel ist es, diese neue Technologie bereits in den kommenden Jahren einzusetzen. Die Forscher arbeiten deshalb eng mit einem Dutzend Entwicklern aus der Industrie zusammen. Dr. Niermann: „Weitere Projekte dieser Art sind in Vorbereitung. Die Technologie eignet sich auch für die Kabinenmontage.“ Und noch ein Vorteil: Ein Montage-Roboter, der über Messdaten gesteuert wird, sammelt alle wichtigen Daten zur Prozessausführung, sodass genau dokumentiert werden kann, wie die Montage eines x-beliebigen Bauteils verlaufen ist.
Kurz vor Marktreife
Der Bereich Automatisierung und Produktionstechnik ist seit 2010 im CFK Valley angesiedelt – in direkter Nähe zum Airbus-Werk in Stade-Ottenbeck. Dort werden Seitenleitwerke und Rumpfschalen aus CFK gebaut. 40 Forscher und bis zu 50 Studenten arbeiten in engem Kontakt zu den Industriepartnern an der Zukunft des Flugzeugbaus. Niermann: „Die meiste Arbeit sitzt im Datenmanagement.“ Was das bedeutet, lässt sich am Beispiel eines handelsüblichen, aber völlig umgerüsteten Roboters veranschaulichen, der auf einem autonomen Bodenfahrzeug montiert ist. Seine Aufgabe: die Bearbeitung eines Bauteils des A320-Seitenleitwerks – eine weltweit einmalige Anlage, die zu einer Produktionssteigerung von 40 Prozent bei gleichzeitiger Platzeinsparung führen kann. Dr. Niermann: „Mit diesem System stehen wir kurz vor Marktreife.“
Wie immer heißt die Devise: schneller, kostengünstiger, effektiver und das bei stabiler Präzision. Denkt man die Strategie konsequent weiter, führt sie in die Automatisierung des Flugzeugbaus. Der Standort Stade spielt dabei eine tragende Rolle.
>> Web: www.ifam.fraunhofer.de